Revolutionizing Steel Machinery- Innovations in Hot Rolling Mills
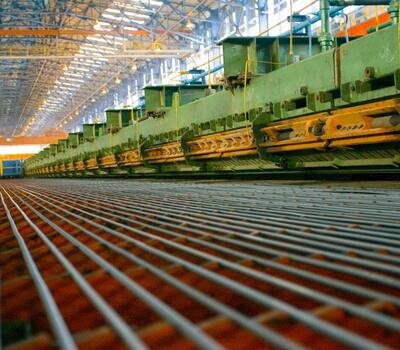
- Advanced Control Systems:
Modern hot rolling mills are equipped with sophisticated control systems that optimize the entire process. These systems incorporate real-time data monitoring, predictive analytics, and automation, allowing for precise control of parameters such as temperature, speed, and tension. The integration of advanced control systems ensures consistent product quality, minimizes defects, and enhances operational efficiency.
- High-performance Rolls:
Rolling mill rolls play a vital role in the hot rolling process. Recent advancements have focused on developing high-performance rolls that offer improved wear resistance, increased durability, and better heat transfer capabilities. Innovative materials, such as carbide-enhanced rolls and composite rolls, have demonstrated superior performance, leading to enhanced productivity and reduced maintenance costs.
- Intelligent Cooling Systems:
Efficient cooling is critical during hot rolling to achieve the desired mechanical properties of the steel. New cooling methods, such as laminar cooling and precision water quenching, have emerged as alternatives to conventional cooling techniques. These intelligent cooling systems ensure precise control over the cooling process, resulting in uniform microstructures and improved material properties.
- Energy Optimization:
Sustainable production practices are a key focus in the steel industry. Hot rolling mills have embraced energy optimization strategies to reduce power consumption and minimize environmental impact. The implementation of energy-efficient motors, regenerative braking systems, and waste heat recovery technologies has significantly improved energy utilization and reduced greenhouse gas emissions.
- Inline Quality Monitoring:
To ensure the highest quality standards, inline monitoring systems have gained prominence in hot rolling mills. These systems employ advanced sensors and imaging technologies to detect surface defects, measure dimensional accuracy, and assess internal quality. Real-time data analysis enables immediate corrective actions, leading to improved product consistency and reduced scrap rates.
- Digitalization and Big Data Analytics:
The integration of digitalization and big data analytics has transformed the way hot rolling mills operate. By collecting and analyzing vast amounts of data from various sources, including sensors, equipment, and production records, manufacturers can identify patterns, optimize processes, and predict maintenance needs. This data-driven approach enhances overall equipment effectiveness, minimizes downtime, and enables proactive decision-making.
Conclusion:
The steel industry is witnessing a technological revolution in hot rolling mill machinery. Advanced control systems, high-performance rolls, intelligent cooling, energy optimization, inline quality monitoring, and digitalization are just some of the key advancements driving efficiency, quality, and sustainability in steel production. These innovations not only improve the productivity and profitability of steel manufacturers but also contribute to a more sustainable and environmentally friendly industry. As technology continues to evolve, the future of hot rolling mills looks promising, with even greater advancements on the horizon.